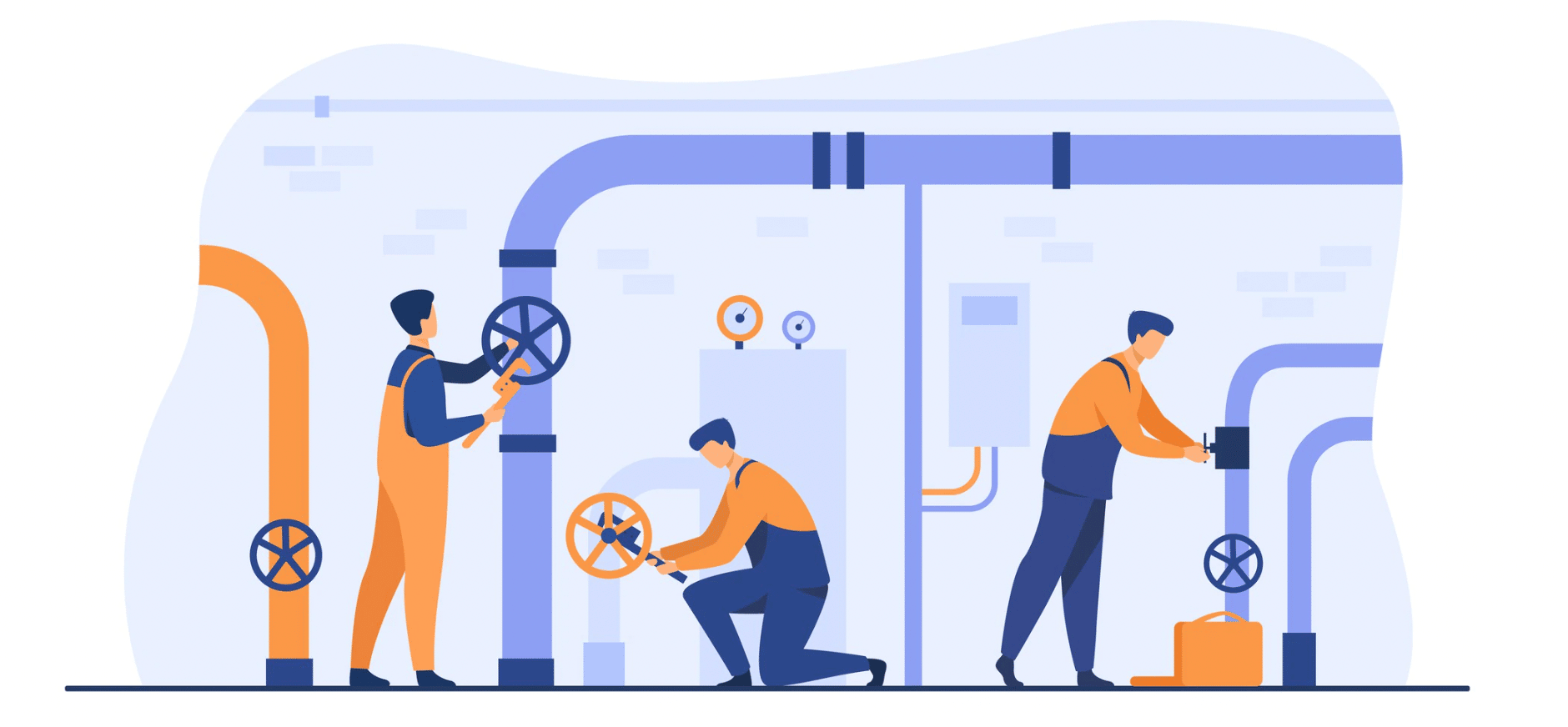
Introduction
The manufacturing industry has long been under pressure to explore and exploit resource efficiency in all areas of the manufacturing process. The goal is to drive profitability and avoid machine downtime, ensuring that output goals can be met, and demand fulfilled.
But the demands on manufacturers do not stop simply because a product has left the factory floor. Customers expect new purchases to work flawlessly, except for regular servicing. Predictive maintenance has the answers to improve customer satisfaction and fulfill manufacturers’ needs. Driven by artificial intelligence (AI) technology and powered by real-time analytics, it can be even more effective.
Just imagine, robots ordering parts they would need in advance to conduct predictive maintenance and remove humans out of the loop!
Table of contents
Also Read: Robotics and manufacturing.
AI Driven Predictive Maintenance
Predictive maintenance is a technique used by engineers in industrial and manufacturing settings to help anticipate when a piece of equipment is likely to fail. As opposed to corrective maintenance, this approach entails preventing asset failures. With the help of specific monitoring tools, maintenance technicians can understand the condition of industrial assets without needing to disrupt their operation. The goal is to fix or replace a part or an entire machine before it fails.
In short, predictive maintenance allows companies to time their maintenance perfectly and improve machine performance. Predictive maintenance systems avoid unplanned downtime due to machine failures, but they also stop businesses from scheduling maintenance routines before it is necessary. Both lead to critical cost savings and allow manufacturing plans to run as efficiently as possible. Done well, predictive maintenance also increases a plant’s productivity and simplifies the management of external contractors.
AI driven predictive maintenance models take the concept of predictive maintenance services one step further. Applying AI technology to the predictive maintenance process allows engineering teams to integrate massive volumes of data into their process and deliver actionable results at the same time.
Better Data Collection
Leading manufacturers have needed to improve productivity and profitability for several years. For example, five years ago, the Organization for Economic Co-operation and Development (OECD) noted that productivity growth for industrial companies across Europe had dropped. Whilst manufacturers had expanded by 2.9% between 1996 and 2005, the OECD only found 1.6% growth in the ten years leading up to 2015.
At the time, consultancy firm McKinsey noted that the companies analyzed by the OECD had left one major asset untapped. In their quest for increased productivity, few companies had taken advantage of information delivered by their own data.
In the five years since the consultants published their assessment, AI technology and business models have developed dramatically. Leading manufacturers today have embraced digital maintenance planning and productivity technology as part of their digital transformation. Real-time data collection and in-depth analysis have been one of the deciding factors in helping predictive maintenance applications succeed where corrective maintenance is not enough.
Those who successfully managed to implement digital solutions have seen profitability increase by up to 10%. However, the consultants still find that these success stories are “lighthouse examples” of automated AI-based predictive maintenance rather than the norm. So, what does it take to limit unscheduled downtime and grow productivity? State-of-the-art AI applications have the answers.
Data Security
The World Economic Forum (WEF) recently declared AI to be the “key to cutting-edge cybersecurity.” The WEF’s experts believe that data security is currently undergoing a major shift. The approach is transitioning from being primarily reactive to becoming more proactive.
The main difference lies in how data security applications learn. Conventional firewalls and other security software products were rule-based. Whenever a new threat was detected, it was added to their database, requiring human intervention.
AI and machine-learning-based algorithms can work smarter and take a more flexible approach at the same time. They start by learning from existing threats, but then take things further by recognizing patterns. Eventually, they can notice new threats without human intervention. As a result, AI becomes more effective in blocking new threats.
Data Integration and Aggregation
One of the main benefits of AI-based predictive maintenance solutions is their ability to process and analyze far greater amounts of data than humans ever could. Not only that, but based on their analysis, algorithms then predict potential outcomes of changes and possible solutions. Just as they are capable of digesting more data, they are also far quicker at comparing future scenarios.
Data integration and aggregation are key enablers of AI. Data aggregation refers to AI’s ability to draw information from different sources. Here is a simple example from a predictive maintenance context: to accurately foresee when a piece of machinery might break, digital tools may start by analyzing data from a specific manufacturing plant. But before making suggestions, they would then collect company-wide or industry-wide information to gain deeper insights.
Data integration is the logical next step. Integration refers to the process of evaluating the aggregated, or gathered, data, summarizing it, looking for failure patterns, and eventually drawing conclusions.
Sufficient data aggregation is a critical prerequisite for successful data integration. Integrated data is necessary to facilitate deep learning and computer vision. Without them, an automated AI-based predictive maintenance system simply cannot operate.
Readiness and Interoperability
Before implementing an AI-based predictive maintenance schedule, it is important to understand the quality of the data a company can access. Predictions based on artificial intelligence algorithms and machine learning models are only as good as the data they are based on.
For that reason, leadership teams need to assess data readiness. Readiness is generally based on two criteria: data volume and data format. The purpose of assessing data readiness is to learn which data you can access easily and how this information can be leveraged to the company’s advantage.
It is equally important to understand what information the organization lacks. Perhaps you are planning to implement a predictive maintenance solution for a product the company has not manufactured before. In that case, it stands to reason that there is hardly any data to rely on. But that does not need to stop you from taking advantage of a predictive maintenance schedule. The team simply needs to look for other sources.
Interoperability refers to the ability of two or more computer systems to work together without disruption. Any business considering predictive maintenance implementation needs to ensure that all data sources can understand each other and communicate with each other.
If systems are operating in so-called silos, without allowing access by others, retrieving their information can be difficult. This kind of lack of interoperability may limit the accuracy of predictive maintenance. Using a single platform that integrates all relevant internal processes can help avoid interoperability issues.
Cost and Expertise
Predictive maintenance is a powerful driver for cost savings in every type of manufacturing industry. No matter whether a business is operating in the B2C or the B2B space, by implementing a well-thought-out AI-based predictive maintenance system, the organization stands to reap considerable benefits.
According to Deloitte, businesses using predictive maintenance tools have these advantages:
Grow equipment uptime by 10 to 20%
Reduce maintenance costs by 5 to 10%
Minimize maintenance planning time by 20 to 50%
The last figure is perhaps the most impressive benefit for manufacturers. Before becoming over-excited, it is critical to remember that AI applications rarely aim to replace human intelligence and expertise. Instead, they are best placed to augment the employee workflow of human engineers. As a result, engineers can focus on tasks that remain too complex for machines.
Looking beyond the employee experience, it is impossible to overstate the role of predictive analytics in improving the customer experience. For example, understanding the failure probability of a product at a certain age could influence the length of its warranty.
Intelligent Solutions
Successful and effective predictive maintenance can only be delivered by intelligent solutions. In this context, that means feeding the algorithm with sufficient high-quality data to help it draw actionable conclusions.
Results alone are not beneficial if they are not giving engineers and their maintenance teams clear guidance on how to act on them. Root cause analysis delivers valuable returns in this respect. Intelligent solutions will also feed back into the original algorithm by comparing the success rate of the initial failure prediction. As the algorithm learns, it will produce more accurate predictions
Saying that, predictive maintenance leaders have set their sights somewhat higher. They are aiming for an automated AI-based predictive maintenance approach, allowing machines to complete autonomous maintenance.
Edge Computing
Edge computing is set to make predictive maintenance applications and implementation faster than ever before. As the world produces ever more data for AI to process and derive actionable insights from, latency and limited bandwidth are starting to cause issues. Companies like IBM predict that the issue will become more pressing as the number of connected devices grows.
Edge computing removes the need for data to be moved to a central server, data center, or the cloud before it is processed. Instead, processing and analysis are done close to the location where the data is being created. Without the time lost to data transfer, meaningful insights become available more quickly. As mentioned above, analyzing sufficient data is essential to delivering actionable insights. More data almost always means more accuracy for predictive maintenance schedules. Edge computing facilitates this type of accuracy without compromising on speed.
Internet of Things (IoT)
With the importance of data quality and volume undisputed, it is time to consider the sources of information. In the context of the digital transformation of industrial maintenance, manufacturers tend to rely on IoT analytics. These advanced analytics are generally driven by sensors that deliver data to the device completing the analysis.
The industrial internet of things (IIoT) is constantly growing, with new devices leading to more effective options. IoT analytics and devices are critical to facilitating deep reinforcement learning. IoT devices are no longer forbiddingly expensive or complex to use. Many are becoming firm favorites with citizen developers.
Also Read: What is the Internet of Things (IoT)?
Predictive Maintenance vs. Preventive Maintenance
Think of preventative maintenance as a classic schedule of maintenance activities. Generally based on time passed or usage, they are a tried and tested form of industrial equipment maintenance. However, preventive maintenance is no longer the best way to respond to the manufacturing world’s demand for efficiency.
Predictive maintenance offers a more intelligent solution by basing maintenance intervals on the actual condition of the asset. This approach takes into account the equipment lifespan and known failure patterns. It is simply a more effective take on asset performance management.
Both approaches aim to eradicate unplanned maintenance and minimize the risk of failure of industrial assets. But predictive maintenance systems have the advantage of using real-time insights to feed autonomous maintenance schedules.
Also Read: Artificial Intelligence the self-designing machine
Conclusion
Automated AI-based predictive maintenance systems will be at the heart of future manufacturing. They help avoid costly asset failures by predicting failure probability and working to drive efficiencies. Intelligent maintenance planning will be a game-changer for customer journeys in the B2B and B2C spaces. The initial implementation will often go more smoothly with the help of reliability professionals who can simplify the organization’s digital transformation.
AI-based predictive maintenance can do more than optimize maintenance planning for industrial assets. Reduced unplanned failures lead to improved safety on the factory floor, and they can also improve a company’s environmental performance.
References
“A Smarter Way to Digitize Maintenance and Reliability.” McKinsey & Company, 23 Apr. 2021, https://www.mckinsey.com/capabilities/operations/our-insights/a-smarter-way-to-digitize-maintenance-and-reliability. Accessed 15 Feb. 2023.
ARC Advisory Group. “Artificial Intelligence for Predictive Maintenance Case Study – Blair Fraser, Lakeside.” YouTube, Video, 31 July 2018, https://www.youtube.com/watch?v=c9fEnbNgn-E. Accessed 15 Feb. 2023.
“Data Aggregation vs. Data Integration (Plus Examples).” Indeed Career Guide, 21 July 2021, https://www.indeed.com/career-advice/career-development/data-aggregation-vs-data-integration. Accessed 15 Feb. 2023.
Dilda, Valerio, et al. “Manufacturing: Analytics Unleashes Productivity and Profitability.” McKinsey & Company, 14 Aug. 2017, https://www.mckinsey.com/capabilities/operations/our-insights/manufacturing-analytics-unleashes-productivity-and-profitability. Accessed 15 Feb. 2023.
Kangas, Santeri. “Why AI Is the Key to Developing Cutting-Edge Cybersecurity.” World Economic Forum, 21 July 2022, https://www.weforum.org/agenda/2022/07/why-ai-is-the-key-to-cutting-edge-cybersecurity/. Accessed 15 Feb. 2023.
“What Is Edge Computing.” IBM, https://www.ibm.com/cloud/what-is-edge-computing. Accessed 15 Feb. 2023.